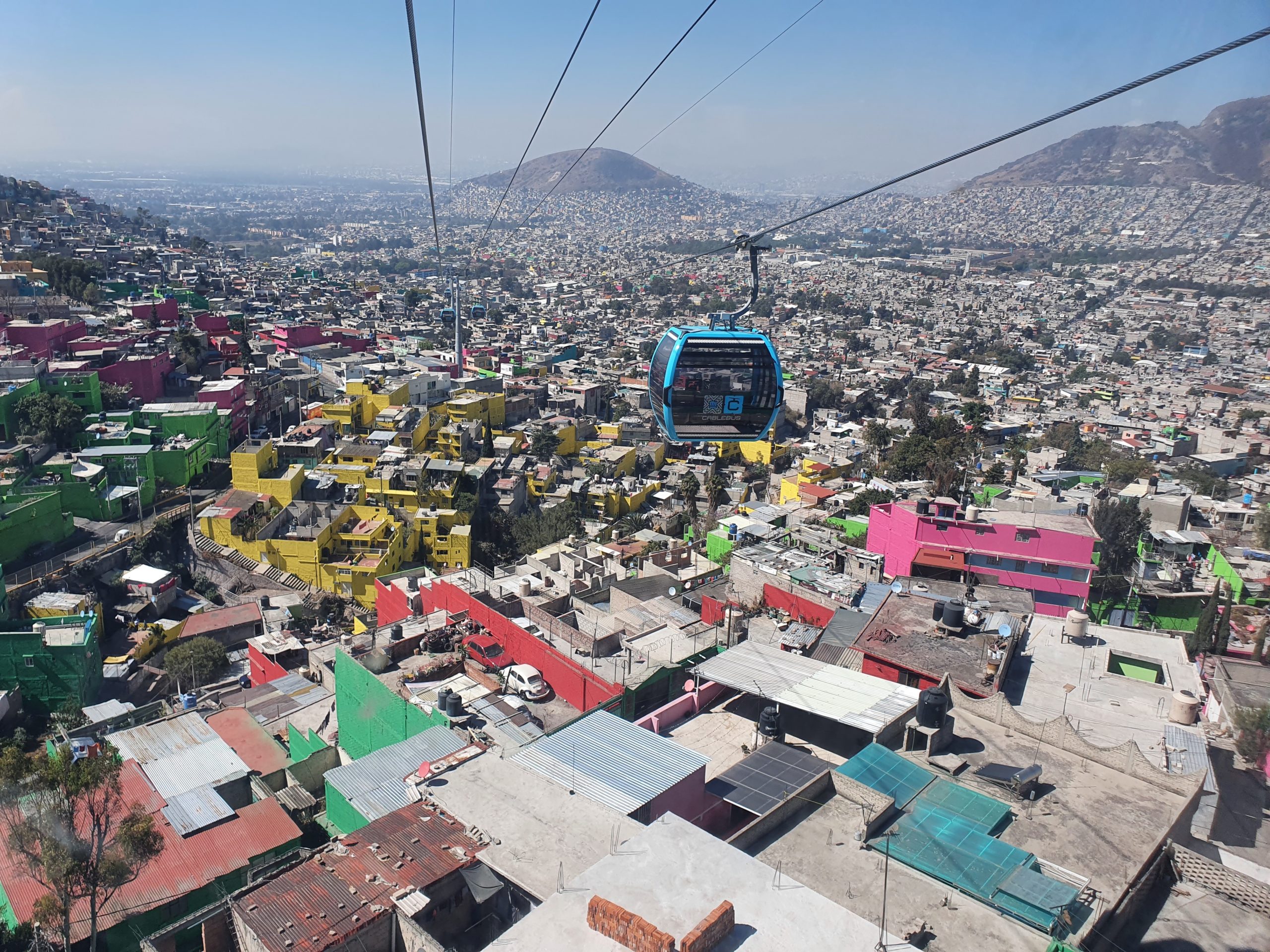
Cities, SI-Urban
The carefree cable car company
Urban cable car operators also have needs: they want high availability of their system and no surprises; the operation and costs need to be predictable. The cable is a critical component here: it must be safe and at the same time require little maintenance.
Low lifetime costs are the aim. To this end, cable car manufacturer FATZER has put together a comprehensive lifetime package for urban cable cars.
A cable car cable is durable only for a period and not permanently: it wears out. Operators must plan the service time of this key component and regularly check the cable to verify the cable condition.
The cable service life can be calculated, and there are criteria to define the discard time, i.e. when the cable must be changed.
Solutions for All Phases
Across all stages in the life of the cable car cable, Swiss manufacturer FATZER has developed solutions that increase the service life of the cable, guarantee safety and reduce costs.
“Our lifetime package turns operators into carefree cable car companies,” CTO Michael Hanimann summarises.
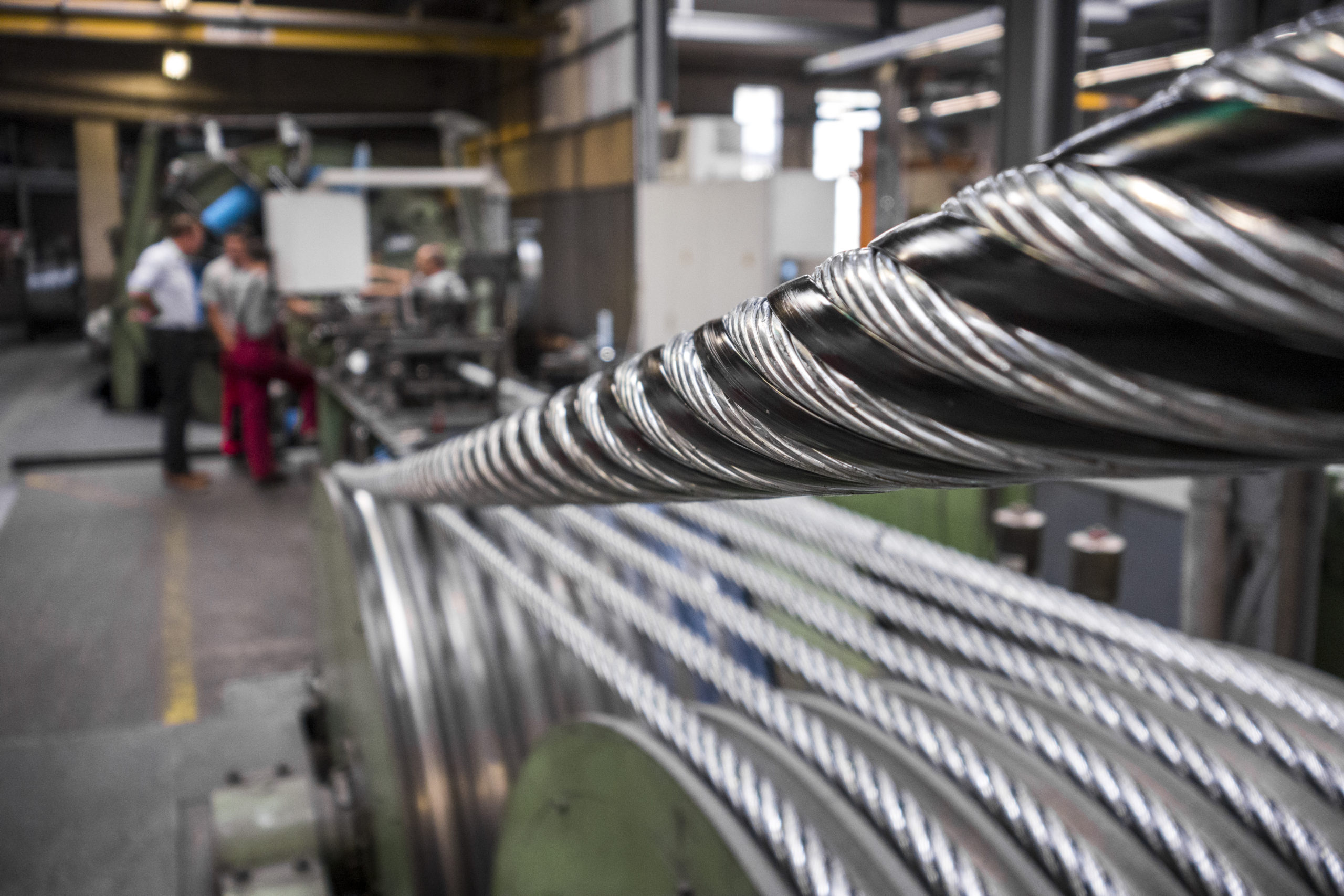
The special cable for urban cable cars is called PERFORMA-DT
Phase 1: Planning
This begins even before production of the cable. FATZER uses its FAROtune software to calculate the service life of the future cable and devises an operating strategy together with the operator.
“Right from the outset we create a digital twin of the cable in the myFATZER.com cockpit, to plan its use, monitoring and operation. The focus here is on predictive maintenance, data exchange and product selection,” Sales Project Manager Philippe Bieri says.
Phase 2: Production
For urban cable cars, FATZER produces the PERFORMA-DT special cable with synthetic profiles between the strands. The cable strands therefore do not touch one another, which significantly increases the service life both of the cable and of the sheaves.
“As a guideline here, we are talking about doubling the service life of the cable in comparison with a standard cable,” Hanimann affirms.
In general, significantly less energy goes into the infrastructure, and this yields advantages in the areas of noise emissions, service life of the supports, and ride comfort.
“The faster the line runs, the greater the customer benefit,” Bieri says.
Moreover, the PERFORMA-DT runs very smoothly: the cable barely vibrates, the elongation behaviour is minimal, the diameter remains constant. The cable elongation is therefore calculable and predictable; shortening is required only in the middle of the service life.
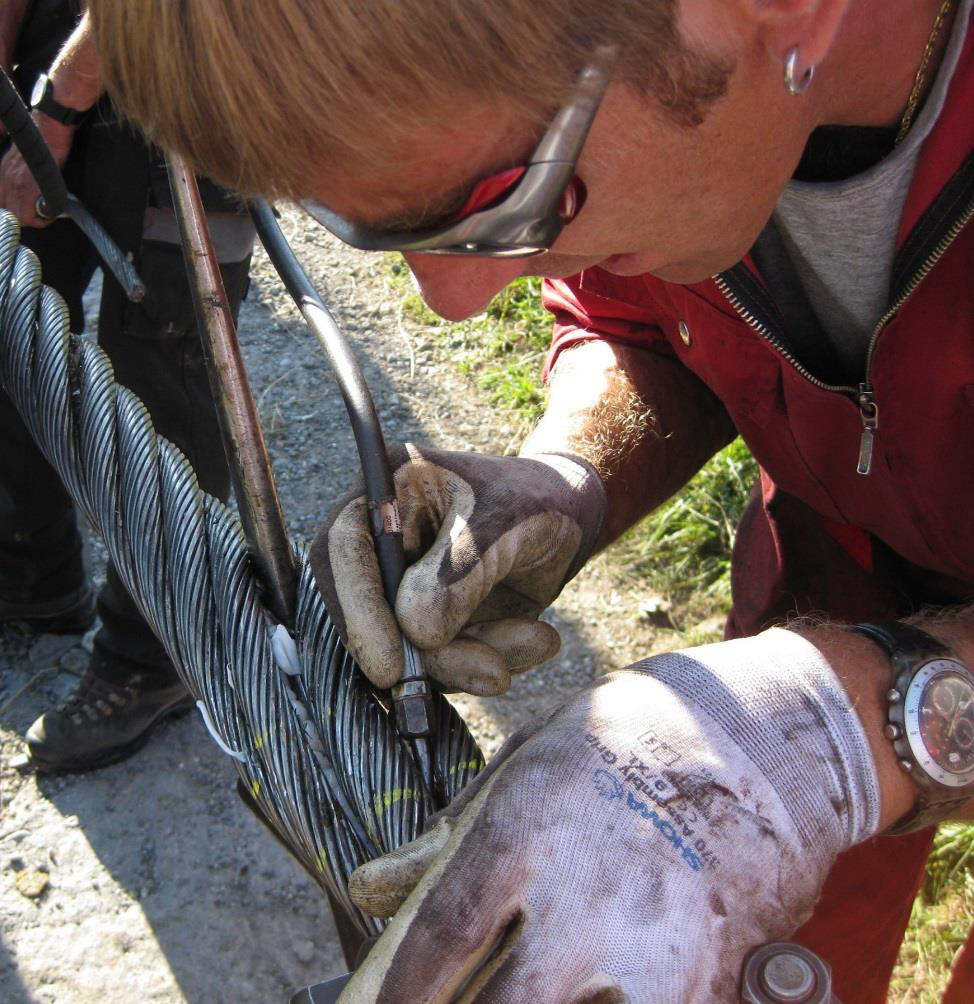
FATZER installers splicing using the TRUsplice method.
Phase 3: Installation
For the PERFORMA-DT to play to its strengths, cable specialists are needed for installation. The splicers from FATZER have many years of experience with their TRUsplice method. With this, the cable is put together on site in the highest quality hand craftsmanship.
The results are: reduced operating costs, longer splice durability and greater availability of the cable car. Thanks to the careful splicing, the line runs more smoothly and the coupling processes in the area of the splice are gentler.
“If they use the TRUscan monitoring system, operators can also save on spliced-in pieces and on travel to an external cable inspector,” Bieri reports.
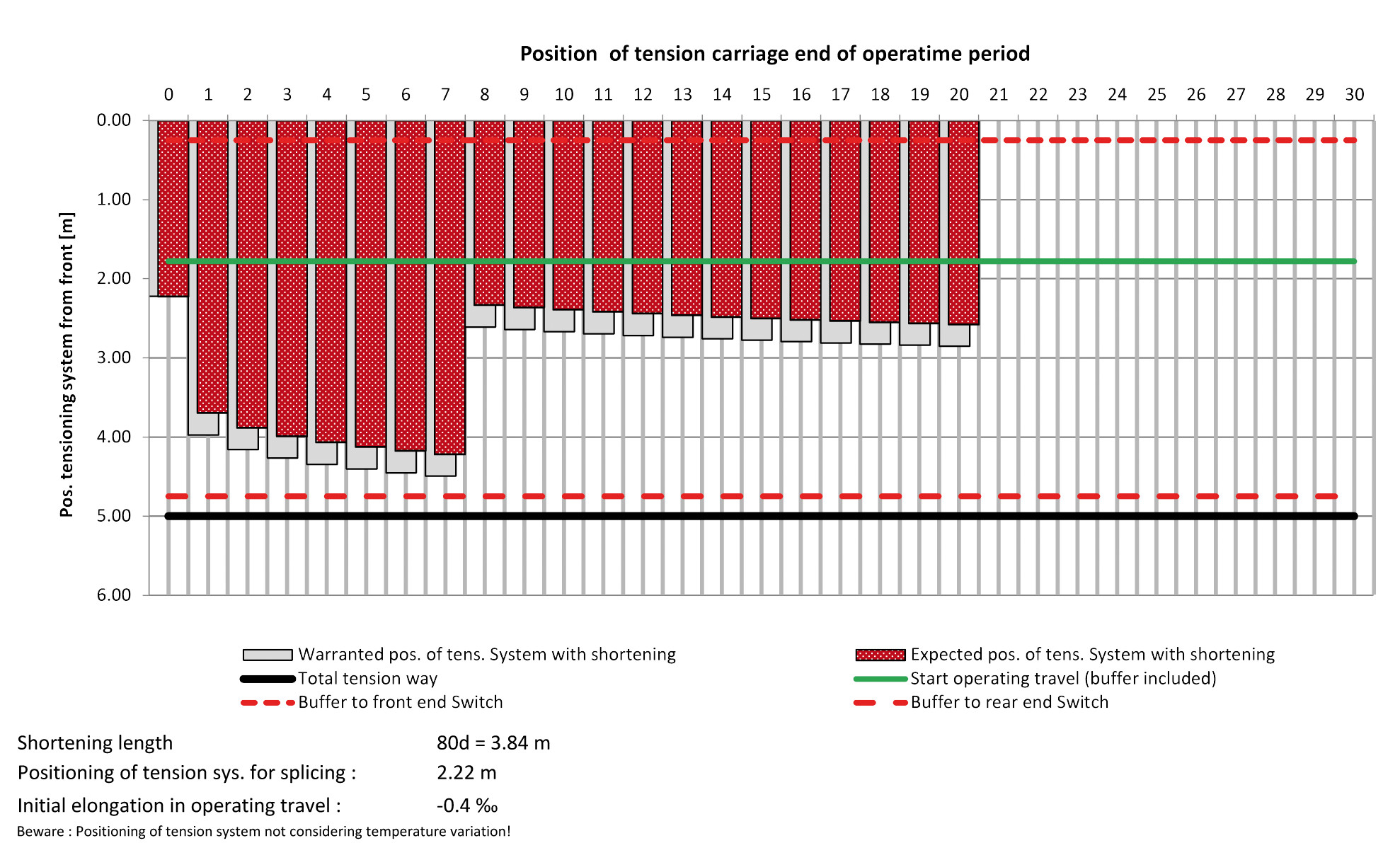
Together with the operator, FATZER devises an operating strategy with FAROtune.
Phase 4: Monitoring
As soon as the cable is running, it must be monitored. Operators can hand over this complex and time-consuming task to FATZER. Automatic and constant monitoring is performed by the TRUscan system and certified specialists.
“TRUscan includes complete handling of the inspection reports required for operation of the system, forecasting of the cable discard time, and monitoring of the cable condition,” Hanimann says.
Safe operation with predictive maintenance is therefore possible with no compromises and no surprises.
Phase 5: Service
If maintenance work appears necessary, the experts from FATZER are quickly on site anywhere in the world. Bespoke maintenance and service contracts have numerous advantages, above all including calculable costs, guaranteed response and intervention times, and a regional presence. Moreover, customers can be sure of compliance with all safety standards and regulations.
This all improves the reliability and availability of the urban cable car and minimises the risks to operation – both critical factors for the cable car as an urban mode of transport. Customers therefore benefit from minimised downtimes and optimised performance of the systems, Bieri guarantees: “they are carefree cable car companies”
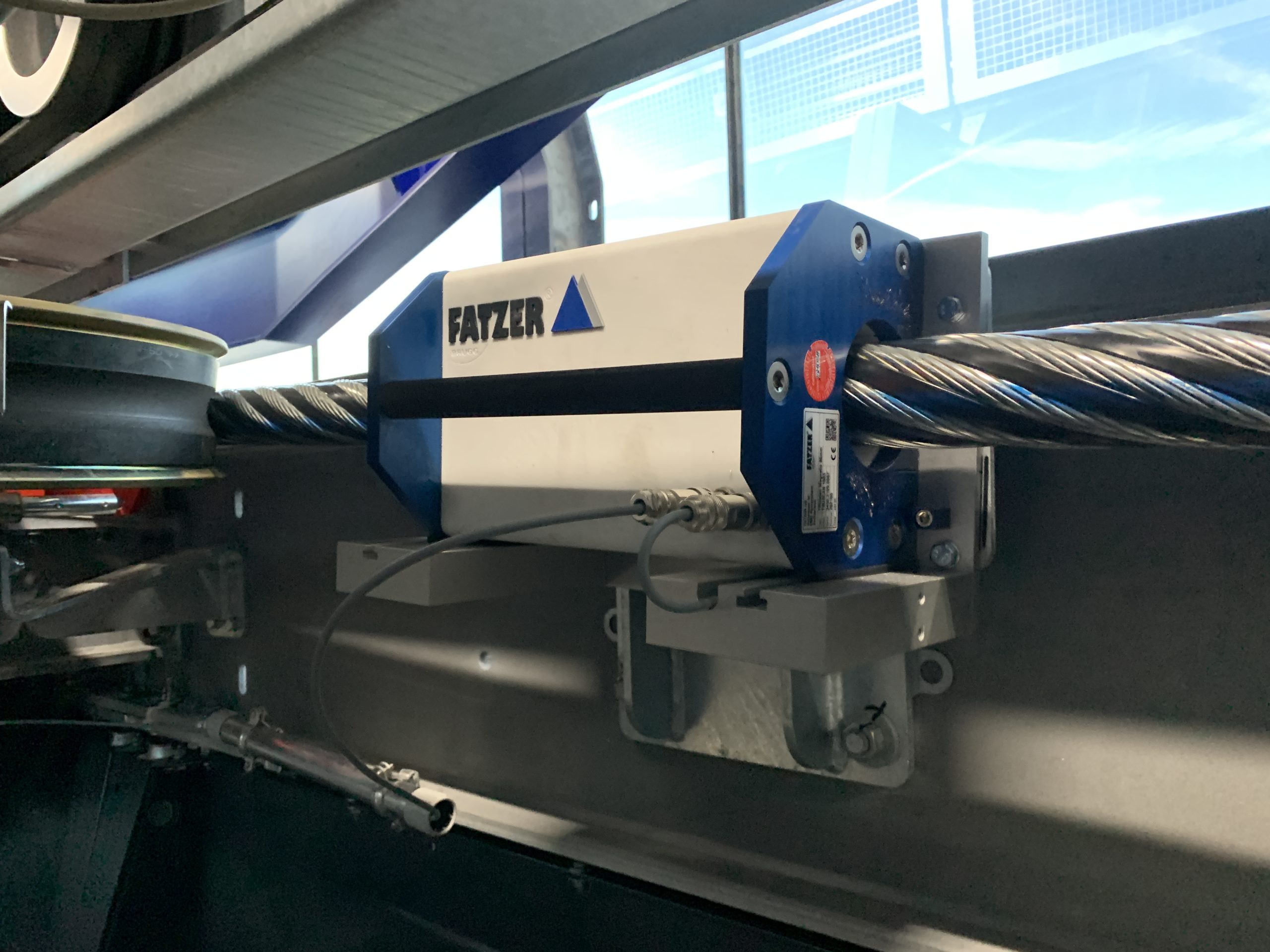
The TRUscan system monitors the cable condition constantly and automatically.