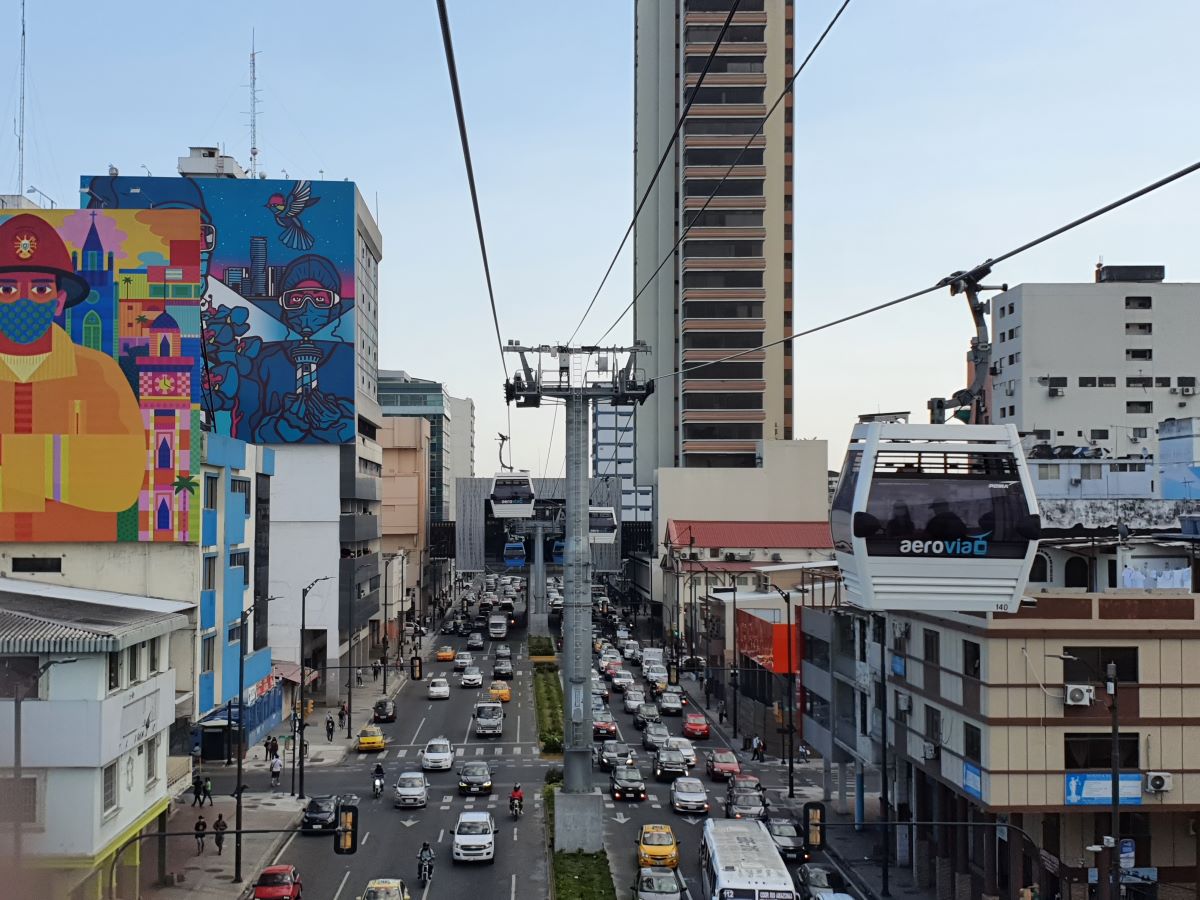
Cities, SI-Urban
The rope as the most important component in urban space
Extreme operating times, high travel speeds, great demands for availability and robustness: urban cable car ropes are exposed to considerably harsher conditions than ropes for classic mountain railways.
For a long time, as urban cable cars are a relatively recent phenomenon, any experience with them was rare.
With the popularisation of urban cable cars since around 2010, however, the level of knowledge has steadily increased. Swiss rope manufacturer FATZER already supplied and looked after many urban cable cars – and was therefore able to identify common challenges.
General challenges
For example, an urban cable car may travel over 6,000 hours per year – twice as many as a heavily used mountain railway in year-round operation. As a form of public transport, the city cable car must often run for over 20 hours per day, 365 days per year.
“Operators understandably have little flexibility for the unexpected,” FATZER Project Manager Philippe Bieri reports.
Maintenance is also a major challenge. This can often be undertaken only at night. Staff generally have around four hours for everyday servicing; larger overhauls require longer lead times.
“Tight space conditions and required road closures also play a role here,” Bieri says.
Moreover, unlike privately operated mountain railways, decisions at short notice are often impossible, for organisational and financial reasons. Municipal or public-private operators often simply need more time here.
“Furthermore, the operators are able to switch from franchised, urban cable cars,” Bieri emphasises. Staff fluctuations are also often high in some countries and there is sometimes only little expertise available.
Challenges for the rope
On complex, urban systems, the rope is under heavy strain. The short distances between the stations – less than one kilometre on average – result in intensive coupling processes and many bending cycles. That means the gondolas are coupled and uncoupled on the rope and the rope is deflected in the stations.
“Both of these are principal causes of wear,” says FATZER Head of Cable Car Technology Oliver Reinelt. The strain can be five or even twenty times greater than on mountain railways: rather than 12,000 bending cycles per year on Alpine systems, 250,000 were counted on urban cable cars.
“The shorter the rope, the faster the wear,” Reinelt summarises. The result of all these challenges is that an urban cable car rope may have to be discarded after only a few years.
Objective: Low lifetime costs
Operators therefore rightly demand an appropriate safety architecture for the rope as well as high availability of the cable car. Surprises and unplanned downtimes are no-go.
“Our priority is high customer satisfaction. This is mainly achievable through low lifetime costs,” FATZER CEO Michael Hanimann reports. The rope manufacturer has therefore developed a long-life package for urban cable car ropes, which prolongs the service life across all life phases, guarantees cable safety and reduces costs.
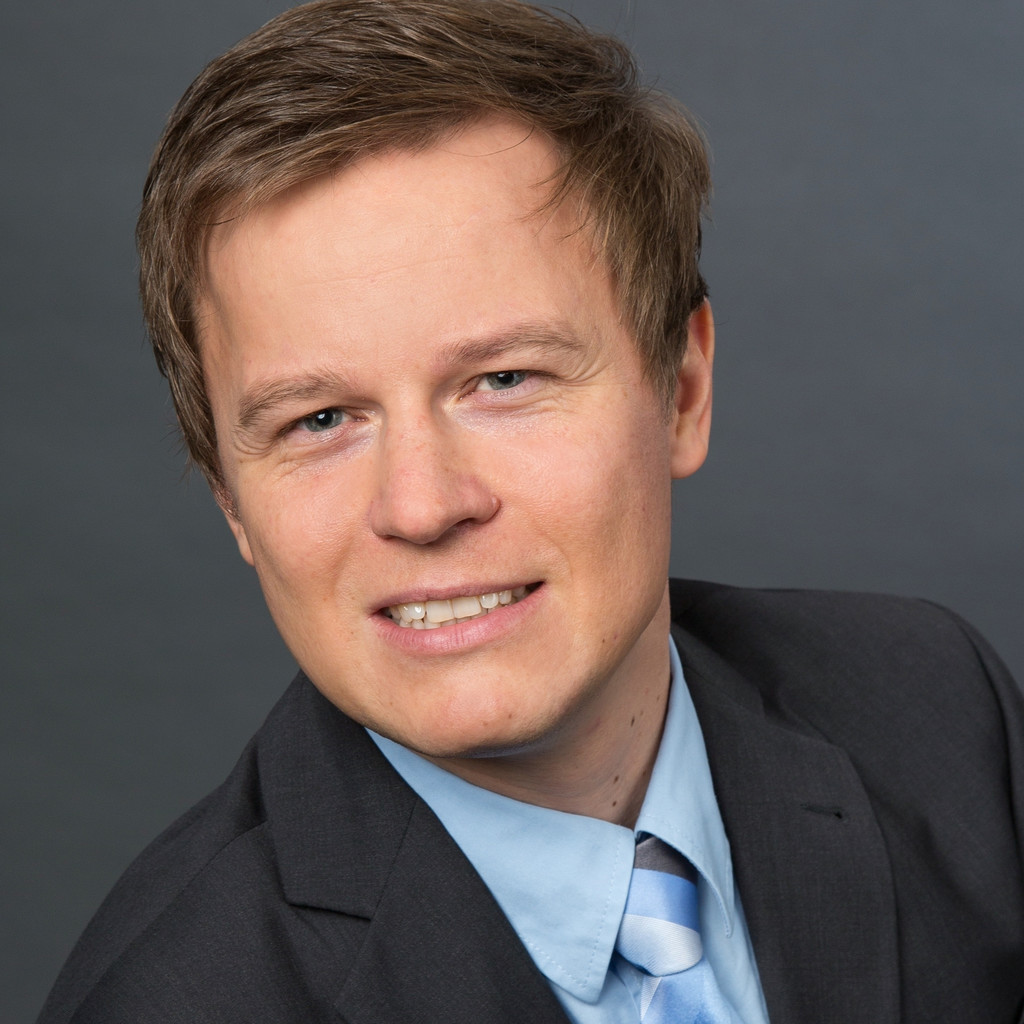
Oliver Reinelt
The FATZER Head of Cable Car technology has a wealth of experience with urban cable cars.
Factor: Planning
This begins even before production of the rope. FATZER uses its FAROtune software to calculate the service life of the future rope and develops an operating strategy together with the operator.
“It is not only the initial investment costs that must be calculated but also the costs of maintenance and replacement,” Hanimann says.
Factor: Product
For urban cable cars, FATZER produces the special PERFORMA-DT rope with plastic profiles between the strands. These prevent the rope strands from coming into contact with one another and fill the “dips” between the strand, significantly prolonging the service life of the rope and rollers.
Factor: Splice
To exploit the strengths of the PERFORMA-DT, rope experts are needed for installation. The splicers from FATZER have years of experience with their TRUsplice method. Here, the rope is joined together with top quality work by hand.
The results: reduced operating costs, longer splice service life and greater availability of the cable car.
The shortened long splice plays an increasingly important role: the socalled TRUsplice ES makes installation cheaper and easier. The shorter long splice means that less scaffolding is required and the splice can ideally be executed in the stations.
Also, the installation time and need for support staff are reduced, and emergency solutions or road closures become unnecessary.
Factor: Control
As soon as the rope moves, it must be monitored. Operators can hand over this complex and time-consuming task to FATZER. Automatic and constant monitoring is undertaken by the TRUscan system and certified specialists.
Safe operation is therefore possible with predictive maintenance, and no compromises or surprises.
Factor: Service
If maintenance work seems necessary, the experts from FATZER can be on site quickly, anywhere in the world. There are many advantages to bespoke maintenance and service agreements, above all including plannable costs, guaranteed response and intervention times, and a regional presence.
Conclusion
All five factors improve the reliability and availability of the urban cable car, as well as minimising the risks to operation. The lifetime costs therefore remain low.
PERFORMA-DT
The urban cable car rope runs very quietly: it barely vibrates, the elongation behaviour is minimal and the diameter remains constant. Rope elongation is therefore calculable and predictable; shortening is required only in the middle of the service life.
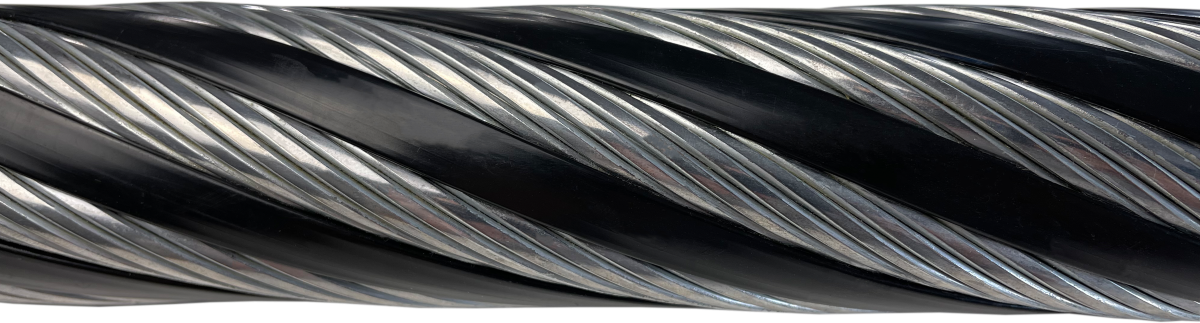