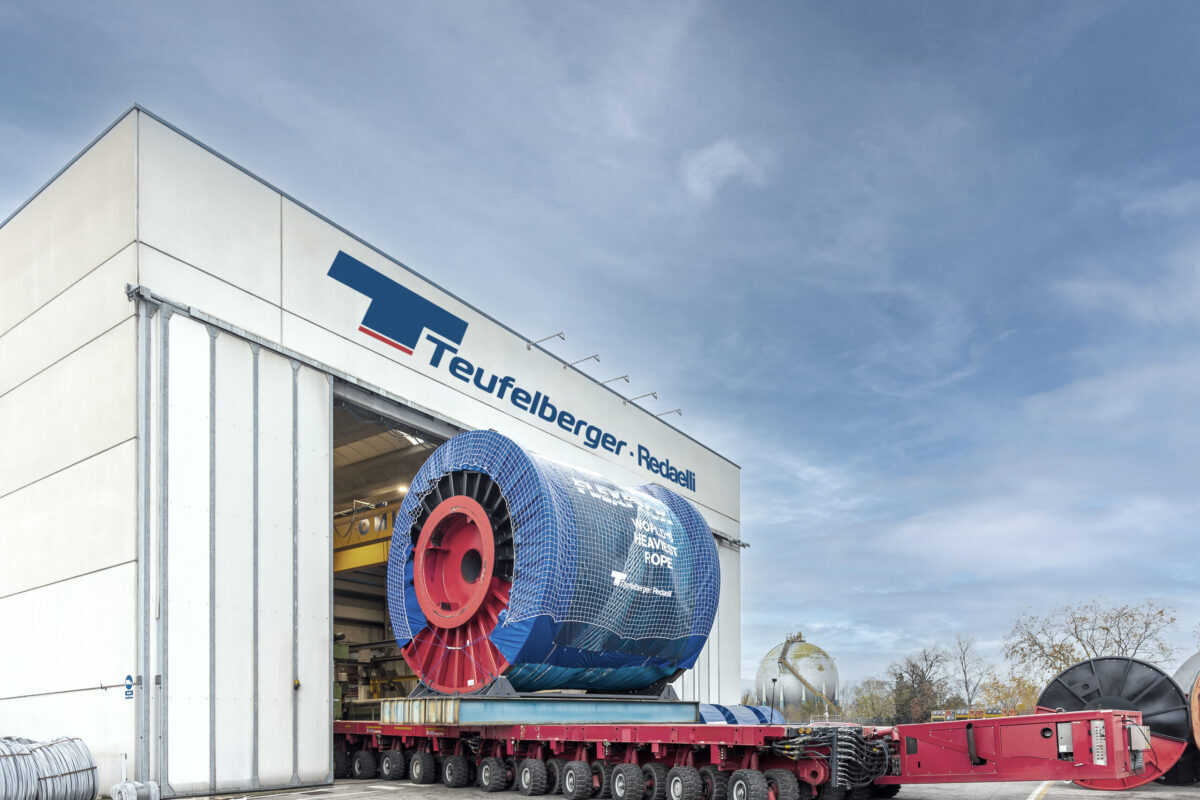
Cities
More capacities for urban cable car ropes
The main goal of the european rope manufacturer TEUFELBERGER-REDAELLI is to perform large and heavy tasks or deliver products for every type of installation worldwide. To achieve this, the international company with roots in Austria and Italy has modernized its plant in Trieste.
Record: world heaviest rope
“From now on, we can produce even larger and heavier ropes. Diameters of up to 70 millimeters and single rope weights of up to 140 tons are possible in the cable car sector, and even more in other industries,“ reports Johannes Smetana, Head of Business Unit Cableways.
It is therefore not surprising that the “Flexpack,“ the heaviest rope in the world, was recently produced. Weighing 495 tons, over four kilometers long, and with a diameter of 160 millimeters, TEUFELBERGER-REDAELLI has secured the Guinness World Record for the rope used in the offshore industry for the fifth consecutive time.
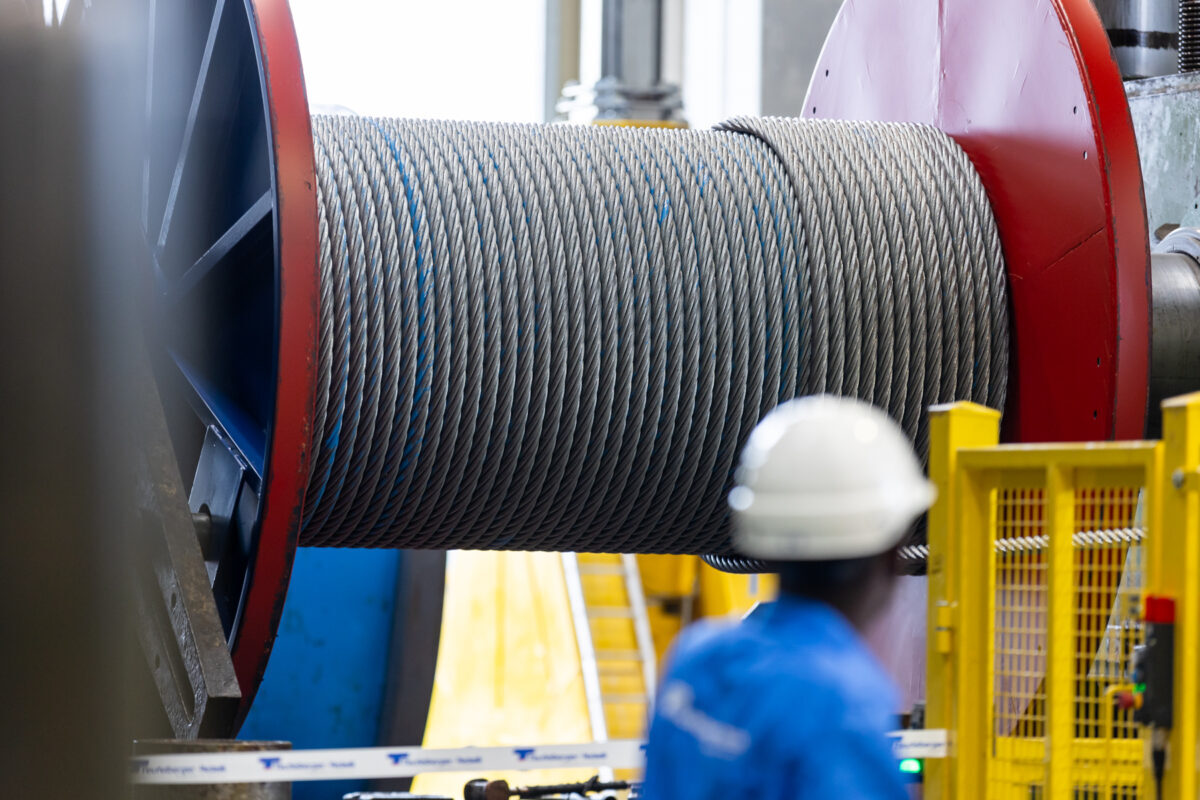
More capacity for cable cars
“Such heavy products are not necessary for urban cable cars, but the trend towards long rope spans with few supports requires long and heavy ropes,“ emphasizes Smetana. Diameters of up to 70 millimeters and 140 tons may indeed be in demand.
That’s why the modernization of the plant in Trieste is so essential, as its production capacity, together with the plant in Gardone, has now doubled from 2,500 to 5,000 tons of rope per year.
Additionally, with direct access to the sea, the ropes are quickly available worldwide. There is also a plant in Austria that produces 2,500 tons of rope per year.
More quality for cable cars
However, TEUFELBERGER-REDAELLI focuses not only on quantity but also on quality. The quality of the ropes has always been a top priority and is continuously improved. The ropes are already inspected during manufacturing through automated geometric measurements.
“Using Geometric Laser Detection (GLD), we measure waviness, stroke length, ovality, and diameter of the rope,“ describes Smetana.
The results are delivered as a report along with the rope. “GLD has significantly improved the quality of the ropes, which directly affects the availability of cable cars in urban areas,“ emphasizes Smetana.
Full-service provider
TEUFELBERGER-REDAELLI handles the rope transportation.
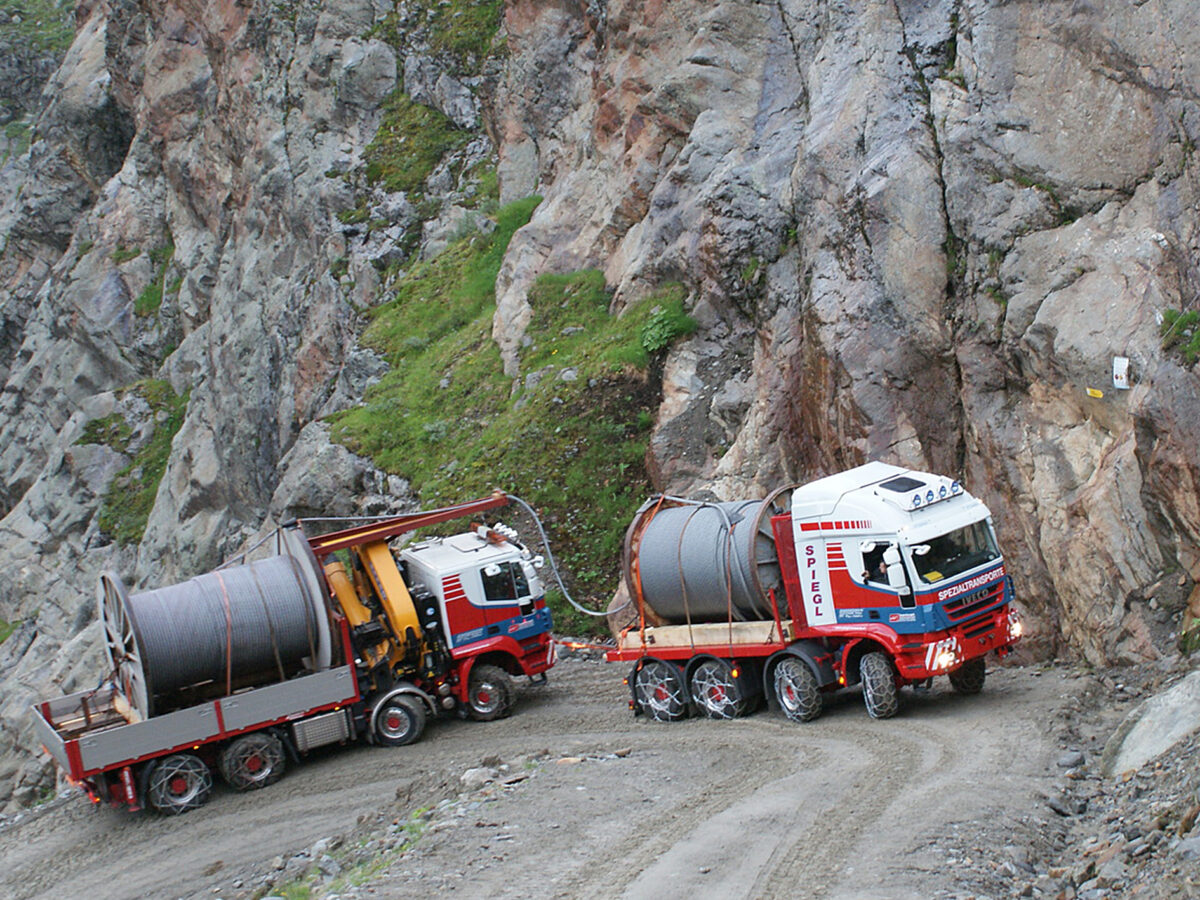
More service for cable cars
TEUFELBERGER-REDAELLI sees itself not only as a pure rope supplier but rather as a full-service provider from inquiry to installation. Together with long-term
experienced partners, the company handles the rope transport. Longer ropes are transported using two reels on two trucks, so the rope does not have to be cut and then laboriously reassembled.
Speaking of assembly: The splicing ofthe ropes is handled by two in-house teams along with worldwide partners. About 500 service interventions per year demonstrate that TEUFELBERGER-REDAELLI takes this step very seriously, as the splice is the weakest point of a cable car rope.
Splicing
The splicing is also handled by two in-house teams from TEUFELBERGER-REDAELLI.
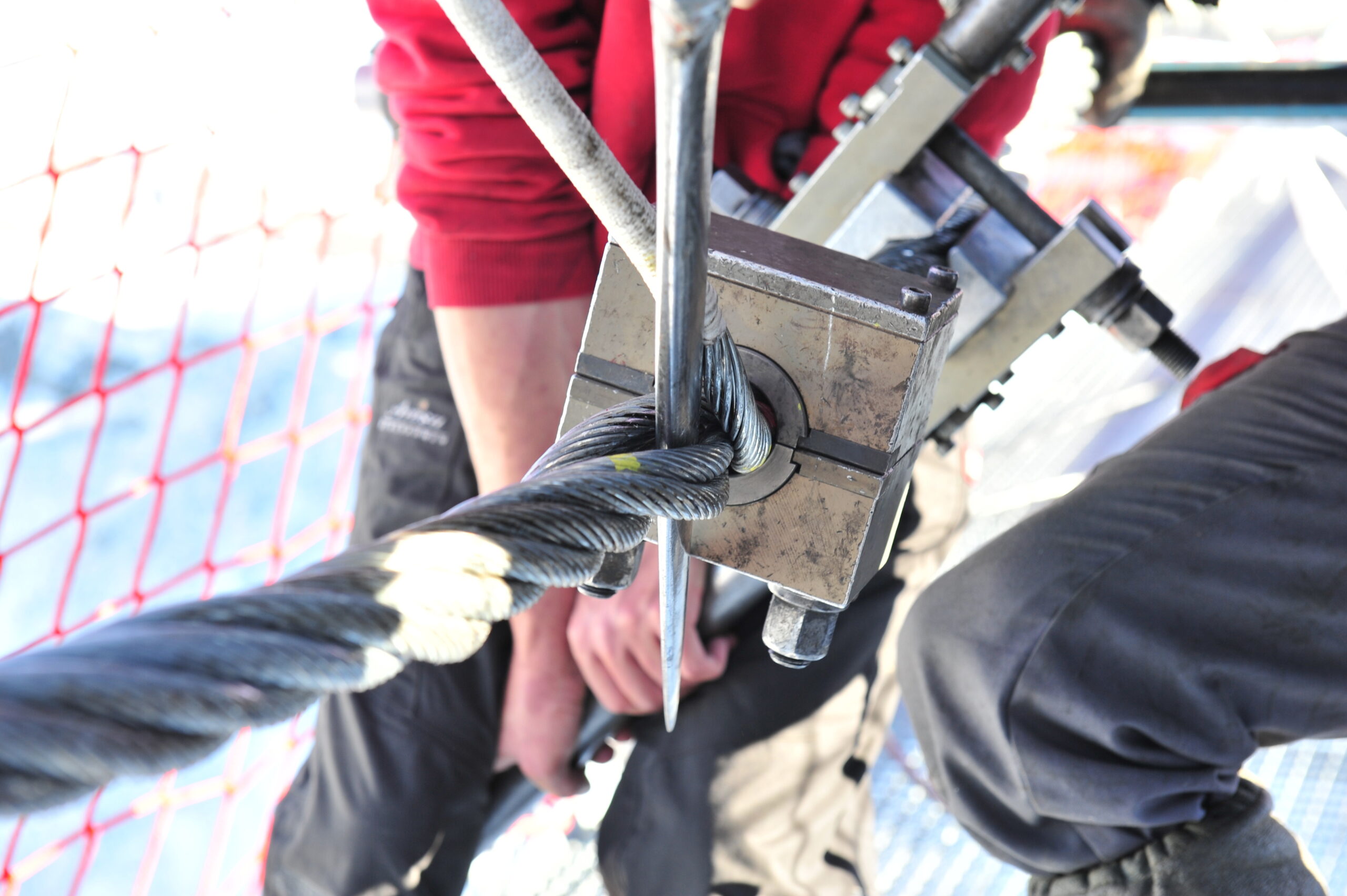
The company also offers the rope pulling service worldwide in collaboration with partners. Only specialized companies have the necessary equipment and know-how to pull ropes properly. Generally, the rope manufacturer organizes the various trades involved in the assembly of the rope.
This means a significant relief for customers and (future) operators of urban cable cars. Last but not least, TEUFELBERGER-REDAELLI is currently working on product innovations in the urban sector, following the motto: “Stressfree through the city!“