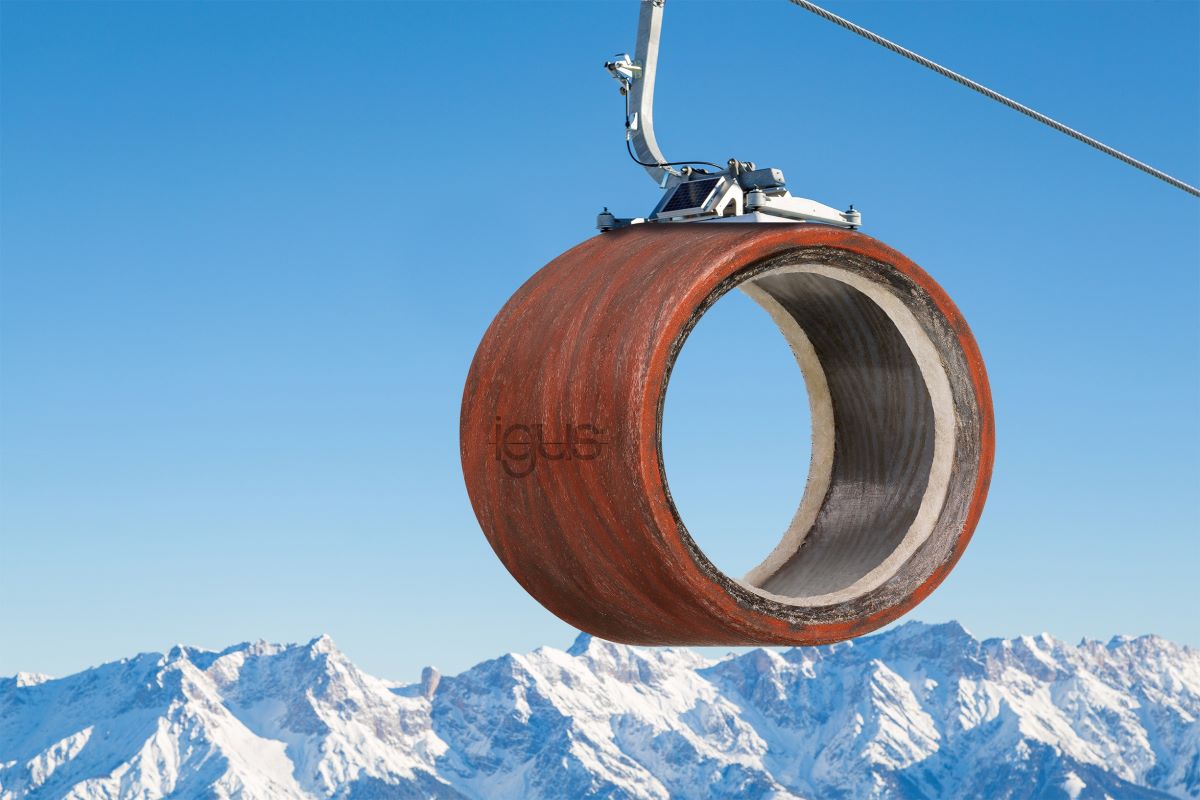
SI 7/2022, Wartung & Service
Weniger Wartungsaufwand dank Polymerlager
Betreiber von Seilbahnen kennen das Problem: Das ständige Nachschmieren hunderter Lagerstellen kostet Zeit und Geld.
Gleichzeitig müssen die Lager herausfordernden Witterungsbedingungen wie Schnee, Wind, Wasser oder Schmutz sowie hohen Belastungen durch den kontinuierlichen Transport von Fahrgästen standhalten.
Die Lösung von igus: Metalllager durch Heavy-Duty-Polymerlager ersetzen. Dafür hat der Kölner Kunststoffspezialist die Werkstoffe iglidur TX1 und TX2 entwickelt. Sie ermöglichen einen langlebigen Trockenlauf ohne Schmiermittel – selbst bei Extremtemperaturen von -60°C.
Ausgangslage
Schmieröl ist vielen Betreibern von Seilbahnen ein Dorn im Auge. Aus mehreren Gründen. Erstens: Das Nachschmieren hunderter Lagerstellen an den Gondeln bedeutet Zeitaufwand.
Als Beispiel seien hier Rollenbatterien einer kuppelbaren Kabinenbahn genannt, bei der je zwei Rollen über eine Wippe miteinander verbunden und so beweglich gelagert sind.
Eine Arbeit, die allerdings alternativlos ist. Denn vernachlässigen Techniker regelmäßiges Schmieren, entstehen teure und schlimmstenfalls gefährliche Schäden an Wellen und Zapfen.
Zweitens: Es bleibt immer ein Restrisiko, dass Schmiermittel von den Lagerstellen heruntertropft und so in die Umwelt gelangt. Und drittens, ein Kostenfaktor: Der Schmierstoff für alle Lagerstellen einer Seilbahn geht ins Geld.
Schließlich benötigen Seilbahn-Betreiber nicht einige Gramm, sondern schnell mehrere Kilogramm pro Jahr.
Lösung
Der Kunststoffspezialist igus aus Köln entwickelt und produziert seit über 30 Jahren Gleitlager aus Hochleistungskunststoffen, die einen reibungsarmen und verschleißfesten Trockenlauf ohne Schmiermittel ermöglichen.
Die meisten dieser Polymerlager, die branchenübergreifend zunehmend Metalllager ersetzen, entstehen dabei im Spritzgussverfahren. igus hat mittlerweile über 60 Werkstoffe für unterschiedlichste Anwendungsfälle im Sortiment.
„Für Seilbahnen benötigen wir allerdings Polymerlager, die besonders hohen Belastungen und regelmäßigen Schwingungen standhalten – und das bei Wind und Kälte, Schmutz und Schnee. Um diesen Ex-tremanforderungen gerecht zu werden, haben wir gewickelte Gleitlager aus den Werkstoffen iglidur TX1 und TX2 auf den Markt gebracht, die bei immer mehr Seilbahnherstellern weltweit zum Einsatz kommen“, sagt Christoph Föttinger, Verkaufsleiter iglidur Gleitlager und Geschäftsleiter von igus Österreich.
Druckfestigkeit bis zu 200 Megapascal
Mit TX1 und TX2 hat igus für Seilbahnen zwei Gleitlagerwerkstoffe aus hochfestem Gewebe entwickelt. Zugfeste Filamente in einer speziell verwobenen Form sorgen für maximale Widerstandsfähigkeit und Formstabilität.
„Mit einer statischen Druckfestigkeit von bis zu 200 Megapascal und einer dynamischen Druckfestigkeit von 140 Megapascal können wir viele Anwendungen in der Seilbahntechnik bedienen – etwa für die Lagerung von Rollenbatterien und Seilklemmen“, so Föttinger.
„Gerade hochbelastete Schwenkbewegungen, bei denen höchste Radiallasten herrschen, sind mit Gleitlagern aus diesen Werkstoffen bestens realisierbar.“
Das Material bewahre seine Widerstandsfähigkeit und Formstabilität dabei auch in rauer Umgebung – in ständigem Kontakt mit Ölen, Chemikalien, Salz und Feuchtigkeit sowie bei Extremtemperaturen von bis zu -60 °C.
Somit müssen sich Betreiber von Seilbahnen selbst in harten Wintern keine Sorgen um die Beständigkeit der Polymergleitlager machen. Ein Versprechen, das für TX1 und TX2 gleichermaßen gelte.
Zwei Produkte
Doch wo liegen die Unterschiede? Welcher Werkstoff eignet sich für welche Anwendung? Die Entscheidung hängt maßgeblich von der Beschaffenheit der Wellenoberfläche ab.
So haben Schwenkversuche im hauseigenen, 3.800 Quadratmeter großen Labor in Köln gezeigt: Gleitlager aus iglidur TX2 sind in Verbindung mit hartverchromten Wellen bis zu 3,5-mal verschleißfester als Gleitlager aus TX1.
Auf einfachen Wellen, etwa auf Modellen ohne Oberflächenbehandlung oder -beschichtung, liefern hingegen Lager aus iglidur TX1 bessere Ergebnisse.
Erhältlich sind die Hochlast-Polymerlager in Durchmessern von 20 bis 80 Millimetern. Als Sonderbauteil auch mit bis zu 2.800 Millimetern.
Zeitintensive Schmierarbeiten vorbei
Polymergleitlager aus iglidur TX1 und TX2 ermöglichen über Jahre einen reibungsarmen Trockenlauf – ohne einen einzigen Tropfen Schmieröl. Denn igus integriert in das Material Festschmierstoffe, die sich im Laufe der Zeit automatisch freisetzen.
Zeitintensive Einsätze für Nachschmierarbeiten gehören deshalb der Vergangenheit an.
Ebenso können Betreiber durch den Wechsel von Metalllagern auf Polymerlager auf Zentralschmierungen verzichten, die Lagerstellen über Schmierleitungen kontinuierlich mit Schmierfett versorgen. Systeme, die oft teuer und wartungsintensiv sind.
Der einzige Nachteil des Schmiermittelverzichts: Es existiert keine Fettschicht mehr, die Wellen und Aufnahmen vor Korrosion schützt. Doch auch hier hat igus Lösungen parat. Möglichkeit eins: Wellen mit einer gasnitrierten Oberfläche, die Korrosions- und Verschleißschutz bietet.
Oder Möglichkeit zwei: Anwender führen eine einmalige Initialschmierung der Welle durch und nutzen iglidur Gleitlager, die mit einer Filzdichtung gefertigt sind.
„Diese sorgt dafür, dass das Fett in der Lagerstelle bleibt und nicht nach außen gelangt. Gleichzeitig schützt die Dichtungen vor dem Eindringen von Schmutz.“